The Consulting Engineer’s Guide to Advanced Electric Boiler Technology
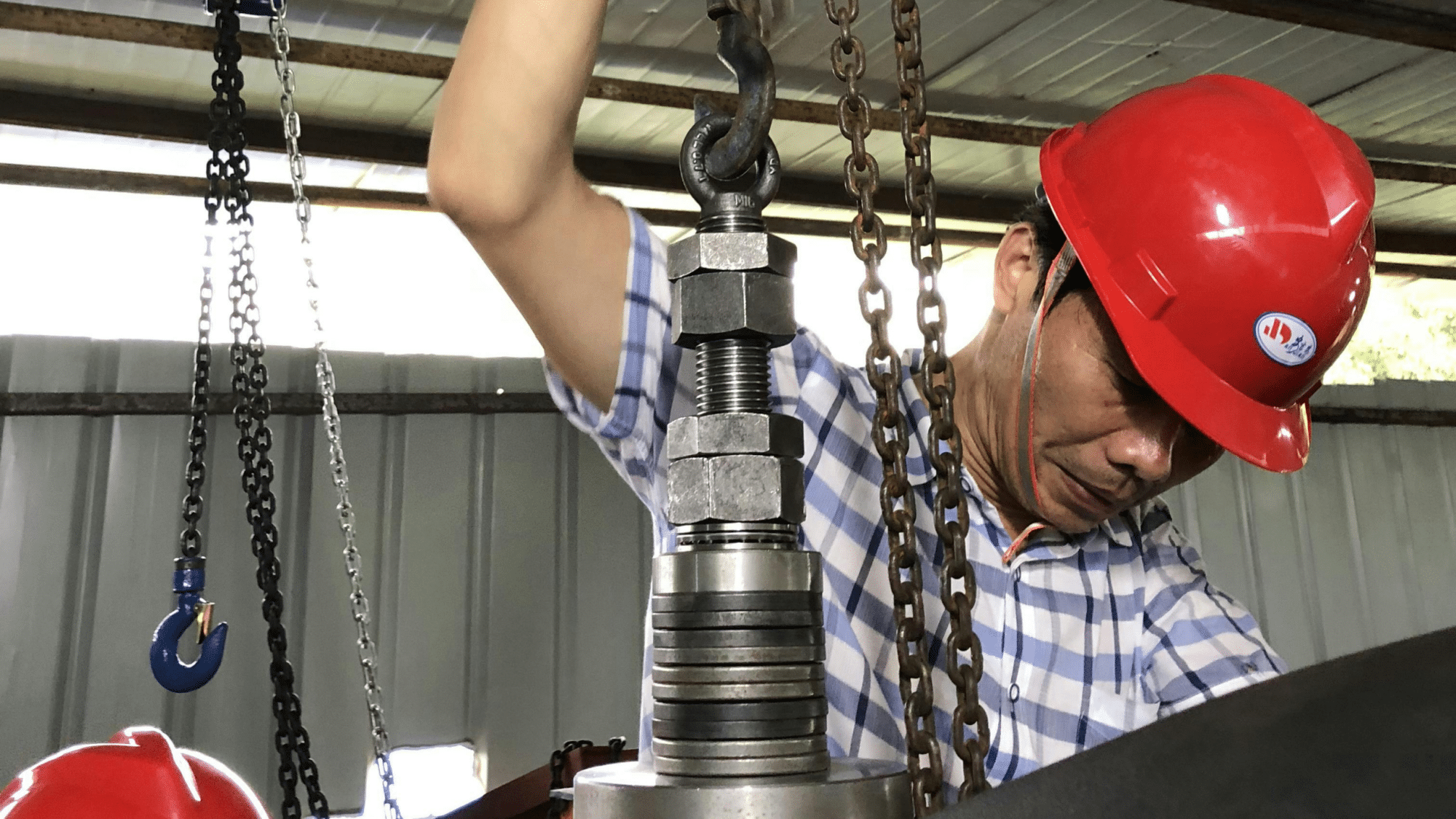
Technology tamfitronics
For consulting engineers tasked with planning, designing, and supervising construction projects for a wide range of industries, advanced electric boilers—particularly high voltage electrode boilers—offer numerous advantages over traditional fossil fuel burning boilers. Due to advances in technology, these boilers can match the capacity (up to 65 MW) and output (270,000 pounds of steam per hour) of traditional gas or oil-fired boilers in a much smaller footprint while converting almost all the energy to heat.
These zero-emission, high voltage electrode boilers are used in diverse environments for applications such as centralized heating, power plants, nuclear stations, swing-load balancing, solar/wind energy consumption, and fuel boiler replacement.
Acme Boilers
Today, there is growing interest in utilizing a new generation of these boilers as an environmentally friendly decarbonization solution. Companies across the globe are considering using electric boilers to become carbon neutral in alignment with COP26 UN Climate Change Conference targets. The transition to electric boilers also aligns with US goals to achieve a carbon pollution-free power sector by 2035 and net zero emissions economy by 2050.
Electric boilers are emerging as more environmentally friendly solutions than traditional gas-fired units that emit not only the notorious greenhouse gasses carbon dioxide (CO2) and methane (CH4), but also dangerous nitrogen oxides (NOx), carbon monoxide (CO), and nitrous oxide (N2O), as well as volatile organic compounds (VOCs), sulfur dioxide (SO2), and particulate matter (PM).
“Communities and businesses appreciate the eco-friendly nature of ultra-efficient, electric boilers. Without combustion, these boilers are safe, clean, and emission free. The design eliminates many environmental issues associated with fuel burning boilers, such as fuel fumes, fly ash, and large obtrusive exhaust stacks,” says Robert Presser, Vice President of Acme Engineering, a manufacturer of industrial and commercial boilers.
However, the challenge for consulting engineers is that many have experience with gas-fired boilers but are less familiar with the selection and implementation of advanced electric boilers, especially the high voltage, high-capacity alternatives available today.
To bridge the knowledge gap, boiler technology expert Robert Presser explains what consulting engineers most need to understand about electric boiler technology, including its selection, implementation, and benefits. Acme, which has operations in the US, Canada, and Europe, provides state-of-the-art boilers and accessories for some of the world’s most renowned companies including Siemens, Toshiba, Bechel, PG&E, Power & Mine, and Hydro Quebec.
Types of Electric Boilers
The first factor to consider in selecting an electric boiler is how much capacity will be required by the user, business, or community.
According to Presser, lower voltage (480 KV) electric resistance heating element boilers are economical, compact, reliable sources to produce steam or hot water for industrial use. The units are well suited to supply these resources at lower capacities, from 9 to 3,600 kW.
However, there are design limitations when heating element boilers exceed 4 MW in capacity, as numerous flanges, elements, contactors, and fuses are typically necessary to function properly. The considerable amperage involved also requires expensive bars for distribution, step-down transformers, and large switch gear.
To avoid these complications at capacities of 4 MW or higher, high voltage jet type and immersed electrode boilers were developed.
High Voltage Electrode Boilers
In the high voltage category, electrode boilers consist of two basic types: immersion and water jet.
In resistance element type boilers, current flows through a resistance wire, which generates heat. The heat is transferred through the element’s sheaf and into the water by conduction to produce hot water or steam.
“With the immersed electrode design, electric current is passed through the water from the electrodes to the counter electrodes [grounded via the vessel’s shell]. The more direct the exposure between counter electrode shield and the electrode, the greater the current draw [amperage] and the more power is produced in hot water or steam,” explains Presser.
Modern jet type electrode boilers utilize the conductive and resistive properties of water to carry electric current and generate steam. An AC current from the grounded central column to a minimum of one electrode box per phase, using the water as a conductor. Since the water has electrical resistance, the current flow generates heat directly in the water itself.
“The more current [amps] that flows, the more heat [BTUs] is generated, and the more steam is produced,” says Presser.
High voltage jet or immersed electrode boilers directly connect to high voltage supply lines from 4.16 KV – 25 KV. Hot water boilers are filled with treated water to create a closed loop system.
According to Presser, the maximum capacity of the boiler can be adjusted by varying the conductivity, which is determined by the temperature and boiler capacity. Typically, a conductivity monitor is installed in the piping and any adjustments are automatically made with chemical treatment.
When it comes to installation, consulting engineers need to consider whether there is sufficient high voltage power, and if a new transformer will be required.
“For these high voltage electrode boilers, the incoming voltage typically required by code is a 4-Wire, three-phase wye wiring configuration, and the phases must be balanced,” says Presser.
In addition, it is necessary to ensure that there is sufficient available space to bring in and install the electrode boilers. This includes determining that there is adequate access into buildings and elevators as well as enough clearance through hallways and doors. When space is limited, Acme’s Slim Series resistance boilers units are designed to produce ample hot water while easing conversion and installation with an ability to “squeeze through” narrow passageways and fit into smaller spaces without costly demolition.
The Benefits of Electric Boilers
Acme Boilers
For consulting engineers considering the use of electric boilers, there are numerous advantages over gas fired units. These include very high energy efficiency and output control, along with increased safety and other benefits.
Energy Efficiency
Although traditional gas fired boilers are familiar, the design is inherently less efficient than modern electric units. Within this category, the energy efficiency of electrode boiler technology offers extraordinarily efficient power-to-heat generation capability.
“With an electrode boiler, you get out of it what you put into it. Basically, you don’t have a decline in efficiency,” says Presser.
With electrode boilers, almost all the electrical energy is converted into heat with no stack or heat transfer losses. This level of efficiency is not achievable in fuel-fired steam boilers even when using an economizer.
In the case of Acme’s CEJS, which has a boiler capacity from 6MW to 68MW, the electrode boiler operates at distribution voltages from 4.16 to 25 KV. The unit is up to 99.9% efficient at converting energy into heat. The boiler can produce steam in capacities up to 270,000 pounds per hour, with pressure ratings from 75 PSIG to 500 PSIG.
Output Control
High voltage electric boilers also offer superior control of energy output. The control system automatically monitors factors such as water level, steam pressure, conductivity, and electrical imbalances so energy input and adjustment is precise, and virtually immediate.
“In contrast, increasing or decreasing the temperature in a gas fired boiler is a slower process because it takes time for the heat in the boiler to rise or dissipate before reaching the targeted output,” says Presser.
As an example, advanced high voltage electrode steam boilers like Acme’s CEJS can control the capacity progressively from 0%-100% and have a 100% turndown ratio (the ratio between a boiler’s maximum and minimum output). Most gas boilers have a ratio of 10:1 or 5:1, which means the units require a much higher minimum output level to function and take a significant time to reach full capacity.
“With a 100% turndown ratio [in a high voltage jet-type electrode unit]you can leave the boiler in standby at low pressure and bring it to full capacity in about 90 seconds as needed, which no other boiler type can achieve today,” says Presser.
High voltage immersion steam boilers like Acme’s CEJWS can control the capacity progressively from 10%-100%.
“From hot stand-by, both the CEJS and the CEJWS steam boilers reach 100% capacity in one minute,” says Presser. He adds that stand-by insulation losses never exceed 10KW even for large boilers.
Increased Safety
High voltage electric boilers are inherently much safer to use than traditional, combustion-fueled boilers, which can emit harmful vapors, leak gas, and even cause explosions and fires.
“With gas burning boilers, any gas leak can increase the risk of an explosion wherever there are fuel lines, fumes, flames, or storage tanks. So, gas units must be continually monitored or periodically inspected,” says Presser.
In gas-fired boilers, explosions can result in the ignition and instantaneous combustion of highly flammable gas, vapor, or dust that has accumulated in a boiler. The force of the explosion is often much greater than the boiler combustion chamber can withstand. Minor explosions, known as flarebacks or blowbacks, can also suddenly blow flames many feet from firing doors and observation ports, seriously burning anyone in the path of a flame.
Natural gas-fired boiler emissions also pose potential hazards in the form of emissions. In addition, fossil fuel burning boilers can face potentially dangerous operational issues stemming from excessive heat accumulation.
Modern electric boilers eliminate many of these risks, so can dramatically improve both operator and environmental safety.
“With the jet type electrode boilers, there are no combustion hazards because there are no flames, fumes, fuel lines or storage tanks, which minimizes the risk of explosions and fires,” says Presser. In case of an electrical short, the breaker that protects the high voltage circuit trips in a matter of milliseconds, protecting the boiler and the electrical network. There is no chance of electrical mishap or fire from the boiler.
“Electric boilers, and specifically the electrode units, are inherently the safest boiler design today. These units do not need an operator because if anything goes wrong, the breaker trips, preventing further escalation of the issue,” says Presser.
Since the design does not rely on combustion, it does not create emissions that would endanger the operator or environment. In addition, the design eliminates common environmental problems associated with fossil fuel burning boilers such as fuel fumes, fly ash, and large obtrusive exhaust stacks.
Although consulting engineers are experts in their designated fields of expertise, keeping up to date with the latest developments in advanced electric boiler technology can provide significant advantages in providing hot water and steam for a variety of industrial purposes.
Understanding how to select, specify, and install electric bo ilers for the specific situation will conserve substantial energy, space, and resources compared to fuel-fired options. In addition, it will not only facilitate project success but also a safer environment that helps combat global warming.
For more info, contact Robert Presser at Acme Engineering via e-mail: [email protected] or visit Acme on the web at: acmeprod.com/hv-electrode-boilers.
Del Williams is a technical writer based in Torrance, California.
Discover more from Tamfis Nigeria Lmited
Subscribe to get the latest posts sent to your email.