Types of Electrical Switchgears and How to do Routine Maintenance on them
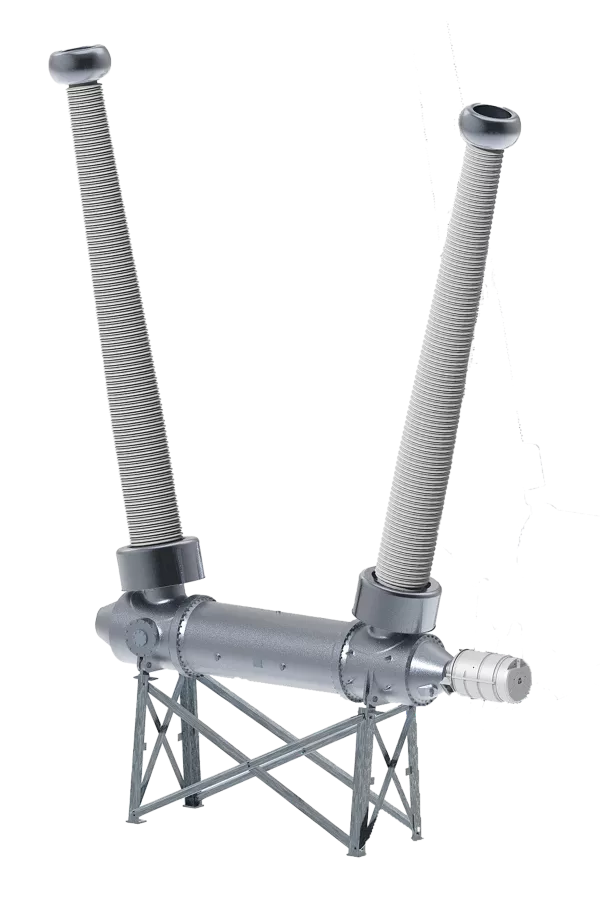
I. Introduction
 - Brief overview of electrical switchgears
An electrical switchgear is a crucial component in the power distribution system, responsible for controlling, protecting, and isolating electrical equipment. It is essential for ensuring the safe and reliable operation of electrical systems by managing the flow of electricity and preventing potential hazards such as overloads, short circuits, and faults. Switchgears come in various types and configurations, each designed to meet specific requirements and applications in different industries and environments. In this section, we will explore the key functions, components, and types of electrical switchgears to provide a comprehensive understanding of their importance in modern electrical systems.
 - Importance of routine maintenance
Routine maintenance is crucial for ensuring the continued functionality and efficiency of electrical switchgears. Regular inspections, testing, and servicing help to identify and address any potential issues before they escalate into major problems. By following a proactive maintenance schedule, users can extend the lifespan of their switchgears and minimise the risk of unexpected failures. Additionally, routine maintenance can also help to optimise the performance of switchgears, ensuring that they operate at peak efficiency and reliability. In the next section, we will discuss some best practices for conducting routine maintenance on electrical switchgears to maximise their longevity and performance.
 - Purpose of the blog post
In this blog post, we will delve into the importance of regular maintenance for electrical switchgears and how it can benefit users in the long run. We will explore the various steps involved in conducting routine maintenance, as well as provide tips and recommendations for ensuring the optimal functioning of switchgears. By implementing these best practices, users can not only prolong the lifespan of their equipment but also avoid costly repairs and downtime. Stay tuned as we uncover the key strategies for maintaining electrical switchgears effectively.
II. Types of Electrical Switchgears
 A. Air Insulated Switchgears
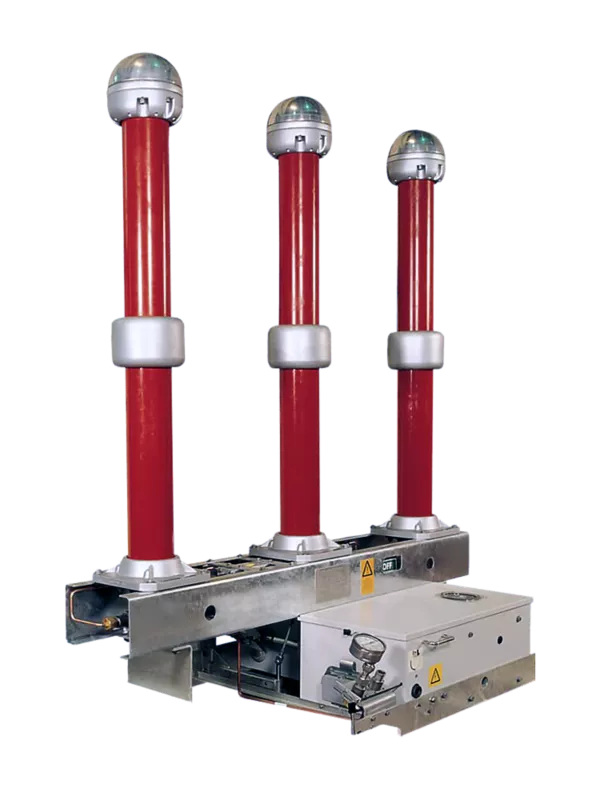
There are several types of electrical switchgears that are commonly used in various industries. One of the most common types is air-insulated switchgear, which use air as the insulating medium to protect the electrical components. These switchgears are often used in medium voltage applications and are known for their reliability and cost-effectiveness. Another type of switchgear is gas-insulated switchgear, which uses sulphur hexafluoride gas as the insulating medium. These switchgears are often used in high-voltage applications and are known for their compact size and high reliability. Other types of switchgears include oil-insulated switchgears and vacuum-insulated switchgears, each with their own unique advantages and applications.
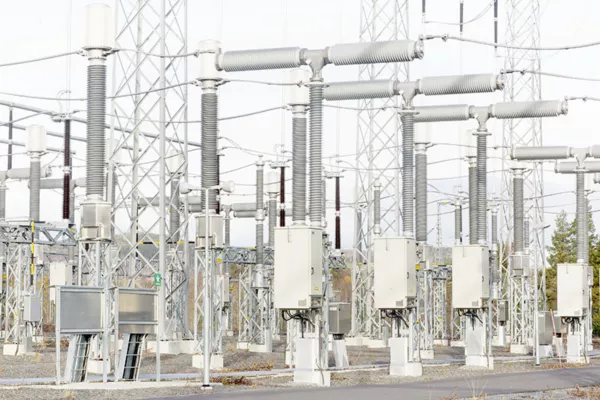
 - Description and components
Switchgears can vary depending on the specific type and design. However, most switchgears typically consist of circuit breakers, disconnect switches, fuses, and protective relays. Circuit breakers are used to interrupt the flow of electricity in the event of a fault or overload, while disconnect switches are used to isolate equipment for maintenance or repair. Fuses are used to protect the circuit from overcurrent conditions, and protective relays are used to monitor the electrical system and initiate a trip signal to the circuit breaker when necessary. Each component plays a crucial role in ensuring the safe and reliable operation of the switchgear system. In the world of switchgear, circuit breakers, disconnect switches, fuses, and protective relays are essential components that work together to ensure the safe and reliable operation of electrical systems. These components play specific roles—from interrupting electricity flow during faults to monitoring the system and initiating necessary actions. Capturing photographs of these components in switchgear installations can showcase their importance in maintaining a well-functioning electrical system.
 - Advantages and disadvantages
of each type of component can also be highlighted through visual documentation, providing valuable insights for maintenance personnel and electrical engineers. Additionally, by visually documenting switchgear installations, potential issues or areas for improvement can be easily identified and addressed before they escalate into larger problems. This proactive approach to maintenance can ultimately save time and money and prevent costly downtime in electrical systems. Overall, the visual documentation of switchgear components serves as a valuable tool in ensuring the efficiency and reliability of electrical systems.
 - Common maintenance procedures
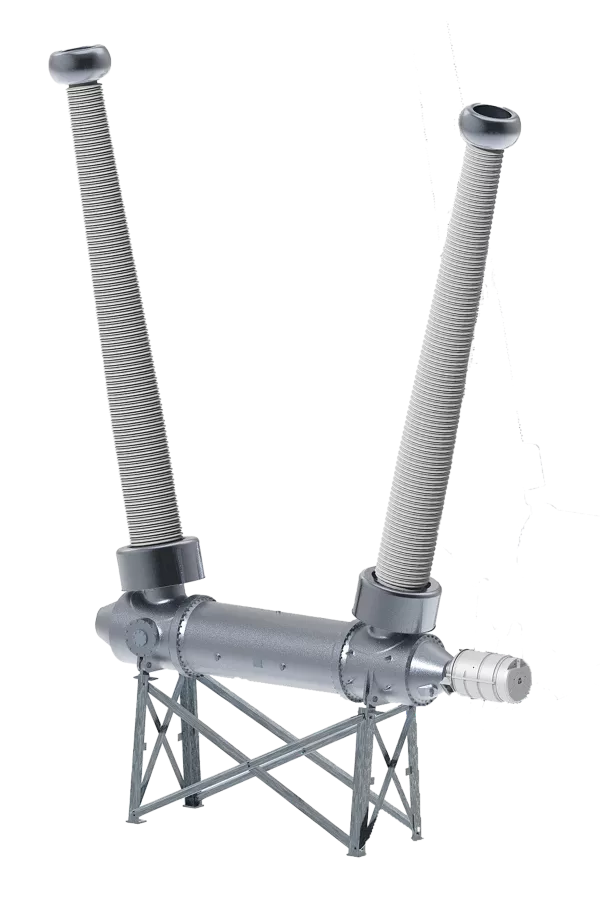
for switchgear components include regular inspections, testing of circuit breakers, and cleaning of contacts to ensure optimal performance. By following manufacturer guidelines and industry best practices, maintenance personnel can prolong the lifespan of switchgear equipment and prevent unexpected failures. In addition, keeping detailed records of maintenance activities and any issues encountered can help track the performance and condition of switchgear components over time. Regular maintenance not only ensures the safe operation of electrical systems but also contributes to the overall reliability and efficiency of the facility. Routine maintenance tasks may include inspecting for signs of wear and tear, checking for loose connections, and testing for proper functionality. These proactive measures can help identify potential issues before they escalate into costly downtime or damage. By investing time and resources into regular maintenance, facility managers can minimise the risk of equipment malfunctions and extend the life of their switchgear systems. Ultimately, prioritising maintenance can lead to improved operational efficiency, reduced downtime, and increased safety for both personnel and equipment.
B. Gas Insulated Switchgears
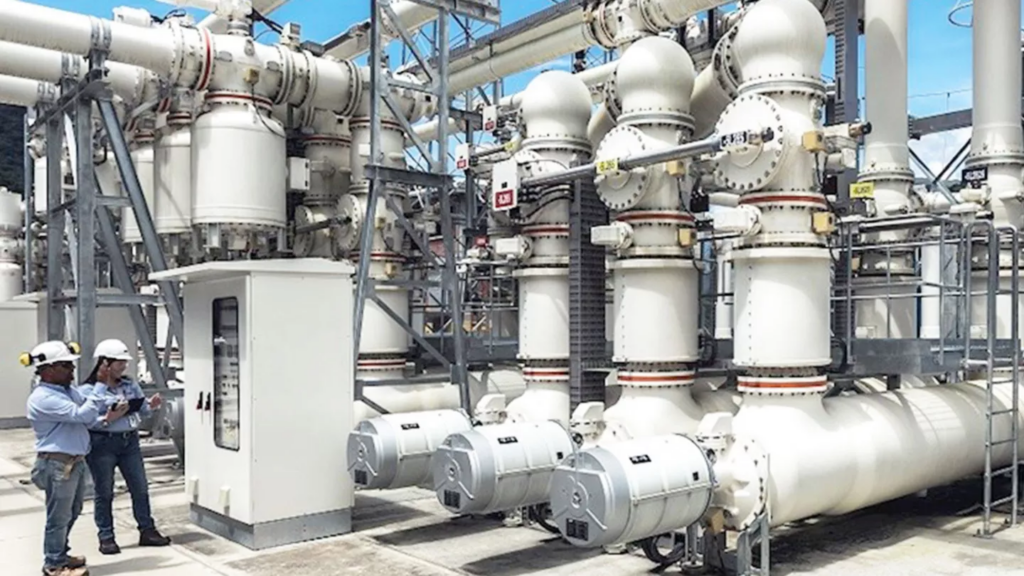
(GIS) are a popular choice for high-voltage applications due to their compact design and reliable performance. Like all electrical equipment, GIS systems require regular maintenance to ensure optimal performance and longevity. Maintenance tasks for GIS systems may differ slightly from those for air-insulated switchgear, but the overall goal remains the same: to keep the system running smoothly and prevent unexpected failures. Some common maintenance tasks for GIS systems include checking for leaks, inspecting insulation, and testing circuit breakers. These tasks should be performed by qualified technicians with specialised training in GIS maintenance to ensure the safety and reliability of the system. For example, a technician may use specialised equipment to detect leaks in the GIS system and repair them promptly to prevent further damage. Additionally, regular insulation inspections can help identify potential issues early on and prevent costly breakdowns in the future.
 - Description and components
of the GIS system must also be regularly reviewed to ensure that all components are functioning properly. This includes checking the condition of circuit breakers and other electrical components to prevent any potential hazards. In addition to these routine maintenance tasks, it is important for technicians to stay up to date on the latest advancements in GIS technology and best practices in order to provide the most effective maintenance services. By staying proactive and thorough in their maintenance efforts, technicians can help ensure the long-term performance and reliability of GIS systems.
 - Advantages and disadvantages
of GIS maintenance outsourcing should also be carefully considered by companies looking to optimise their operations. Outsourcing maintenance services can provide cost savings and access to specialised expertise, but it may also result in a loss of control over the maintenance process. Ultimately, companies must weigh the pros and cons of outsourcing maintenance to determine the best approach for their specific needs and goals. Additionally, companies should regularly evaluate the performance of their maintenance providers to ensure that they are meeting their expectations and delivering high-quality services. By carefully managing GIS maintenance, companies can maximise the efficiency and effectiveness of their systems while minimising downtime and potential risks.
 - Common maintenance procedures
include regularly updating software and hardware, conducting system checks and backups, and addressing any issues or malfunctions promptly. It is important for companies to establish clear communication channels with their maintenance providers to ensure that any problems are addressed in a timely manner. Regular training and development for maintenance staff can also help improve the overall quality of maintenance services and prevent potential issues from arising. In addition, companies should consider implementing preventative maintenance strategies to proactively identify and address potential problems before they escalate. By taking a proactive approach to maintenance, companies can reduce costs, improve system reliability, and ultimately enhance overall business operations. By regularly inspecting equipment and systems, companies can identify issues early on and avoid costly repairs or downtime. This can also help extend the lifespan of equipment and prevent unexpected failures. Implementing a thorough maintenance schedule and keeping detailed records of all maintenance activities can further optimise maintenance processes and ensure that everything is running smoothly. In the long run, investing in proactive maintenance strategies can lead to increased efficiency and productivity for businesses of all sizes.
C. Hybrid Switchgears
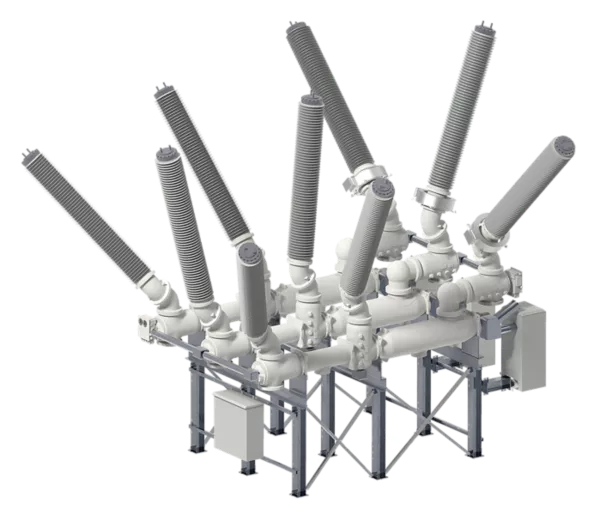
offer a versatile solution for companies looking to improve their electrical distribution systems. These switchgears combine the benefits of both traditional air-insulated and gas-insulated switchgears, providing a reliable and cost-effective option for managing power distribution. With features such as compact design, high reliability, and ease of maintenance, hybrid switchgears are becoming increasingly popular in various industries. Companies that choose to invest in hybrid switchgears can benefit from improved safety, reduced maintenance costs, and enhanced operational efficiency. In addition, these switchgears are designed to meet the specific needs of modern businesses, offering flexibility and scalability for future expansion. Overall, hybrid switchgears are a smart choice for companies looking to upgrade their electrical infrastructure and optimise their operations.
 - Description and components
of hybrid switchgears
Hybrid switchgears combine the best features of both traditional air-insulated and gas-insulated switchgears, offering a compact and reliable solution for electrical distribution. The main components of a hybrid switchgear include a circuit breaker, disconnectors, earthing switches, and current transformers. These components work together to ensure the safe and efficient operation of the electrical system, providing protection against overloads, short circuits, and other electrical faults. Additionally, hybrid switchgears are equipped with advanced monitoring and control systems, allowing for remote operation and real-time monitoring of the electrical network. Overall, the combination of innovative design and advanced technology makes hybrid switchgears a valuable asset for any business looking to enhance their electrical infrastructure.
 - Advantages and disadvantages
The use of hybrid switchgears must be carefully considered before making a decision to implement them in a facility. One advantage of hybrid switchgears is their compact size, which allows for more efficient use of space in electrical rooms. Additionally, the advanced monitoring and control systems can help to quickly identify and address any issues that may arise, minimising downtime and potential damage to equipment. On the other hand, one disadvantage of hybrid switchgears is their higher initial cost compared to traditional switchgears. However, this cost may be offset by the long-term benefits of improved safety, reliability, and efficiency. Ultimately, the decision to invest in hybrid switchgears should be based on a thorough evaluation of the specific needs and requirements of the electrical system in question.
 - Common maintenance procedures
for hybrid switchgears include regular inspections, testing, and cleaning of components to ensure optimal performance. In addition, it is important to follow manufacturer guidelines and recommendations for maintenance to prolong the lifespan of the equipment. Regular maintenance can also help to prevent unexpected failures and costly repairs in the future. By staying proactive and diligent in maintenance efforts, users can maximise the benefits of hybrid switchgears and ensure the continued reliability of their electrical system. For example, a power distribution company regularly schedules inspections and testing of its hybrid switchgear to identify any potential issues before they escalate. By adhering to manufacturer guidelines and conducting routine maintenance, the company has been able to avoid costly downtime due to equipment failures. This proactive approach has allowed the company to maintain a reliable electrical system and minimise the risk of unexpected disruptions in power distribution.
III. Routine Maintenance of Electrical Switchgears
Switchgears are essential components of any electrical system, serving to control, protect, and isolate electrical equipment. Routine maintenance of switchgears is crucial to ensure their proper functioning and prevent potential hazards. Regular inspections, testing, and cleaning of switchgears can help identify any signs of wear and tear, loose connections, or other issues that could lead to malfunctions or failures. By staying proactive in their maintenance efforts, companies can extend the lifespan of their switchgears and maintain the overall reliability of their electrical systems.
 A. Visual Inspection
 - Checking for signs of wear or damage
, such as corrosion, rust, or loose components, is an essential part of switchgear maintenance. Inspectors should look for any visible cracks, leaks, or discolouration that could indicate a problem. Additionally, checking for proper labelling and clear signage on the switchgear can help ensure that operators can easily identify and operate the equipment in case of an emergency. Regular visual inspections should be conducted by trained personnel to catch any potential issues before they escalate into major problems.
 - Verifying connections are secure
and tight is another crucial aspect of switchgear maintenance. Loose connections can lead to overheating, arcing, and ultimately failure of the equipment. Inspectors should carefully examine all terminal connections, bus bars, and cable connections to ensure they are properly tightened and in good condition. Any signs of overheating, such as discolouration or melting of insulation, should be addressed immediately to prevent further damage. Regularly tightening connections and conducting thermal imaging scans can help identify potential issues before they cause downtime or safety hazards. Regular maintenance and inspections are key to ensuring the reliability and safety of switchgear systems.
 - Cleaning switchgear components
can also help prevent dust and debris buildup, which can hinder proper operation and increase the risk of electrical fires. Inspectors should use appropriate cleaning agents and tools to remove any contaminants from the equipment. Additionally, checking for signs of corrosion or wear on components such as circuit breakers and contactors is essential to prevent malfunctions and breakdowns. Proper maintenance of switchgear systems is crucial for maintaining the integrity of electrical distribution networks and preventing costly downtime. Regular cleaning and inspection routines should be implemented as part of a comprehensive maintenance program to ensure the continued efficiency and safety of switchgear equipment.
B. Testing Procedures
 - Insulation resistance testing
is another critical aspect of switchgear maintenance. This test measures the resistance of the insulation material between conductors and ground, helping to identify any potential breakdown of insulation that could lead to electrical faults or equipment failure. Insulation resistance testing should be performed regularly to ensure the reliability and safety of the switchgear system. In addition, power factor testing can be used to assess the condition of the insulation and detect any moisture or contamination that may be present. By following a thorough testing procedure, maintenance technicians can identify and address any issues before they escalate into serious problems.
 - Contact resistance testing
is another important aspect of switchgear maintenance. This type of testing involves measuring the resistance at connection points within the switchgear system, such as at the contacts of circuit breakers or disconnect switches. High contact resistance can result in overheating and arcing, which can lead to equipment failure or even fire. Regular contact resistance testing can help to identify any issues with connections before they become a safety hazard. Additionally, thermal imaging can be used to detect hot spots within the switchgear system, indicating potential problems with connections or components. By incorporating these testing methods into a comprehensive maintenance program, facilities can ensure the reliability and safety of their electrical distribution system.
 - Circuit breaker operation testing
is another crucial aspect of maintaining a safe and reliable electrical distribution system. Circuit breakers are designed to protect the system from overloads and short circuits by interrupting the flow of electricity when necessary. However, if a circuit breaker fails to operate properly, it can result in serious damage to equipment and pose a safety risk to personnel. Regular testing of circuit breaker operation can help to ensure that these devices are functioning correctly and provide the necessary protection to the system. This testing can involve simulating overload and short circuit conditions to verify that the circuit breaker responds appropriately and trips as intended. In addition, routine maintenance of circuit breakers, such as cleaning and lubrication, can help to prevent issues that could affect their operation. By incorporating circuit breaker operation testing into a comprehensive maintenance program, facilities can proactively identify and address any issues before they escalate into costly repairs or safety hazards.
C. Lubrication
 - Lubricating moving parts
of the circuit breaker is an essential aspect of maintenance to ensure smooth operation. Proper lubrication can help reduce friction and wear on components, extending the lifespan of the circuit breaker. It is important to use the correct type of lubricant for each specific component to avoid damage or malfunction. Regular lubrication should be included as part of a routine maintenance schedule to keep the circuit breaker in optimal condition. Additionally, monitoring the condition of the lubricant and replacing it when necessary can help prevent issues and ensure the circuit breaker continues to operate effectively.
 - Checking oil levels in oil-filled switchgears
is another important aspect of maintenance for circuit breakers. Oil-filled switchgears rely on the proper levels of oil to provide insulation and cooling for the components within. Monitoring the oil levels regularly and topping up as needed can prevent overheating and potential damage to the circuit breaker. In addition to checking oil levels, it is also important to inspect the condition of the oil for any signs of contamination or degradation. Regular oil analysis can help identify any issues early on and prevent more serious problems from occurring. Overall, proper maintenance of oil-filled switchgears is crucial for ensuring the reliable operation of circuit breakers and preventing costly downtime.
 - Replacing worn out lubricants
is another important aspect of maintaining oil-filled switchgears. Over time, the lubricants can break down and lose their effectiveness, leading to increased friction and wear on the components. By regularly replacing worn-out lubricants, you can help prolong the life of your switchgear and prevent unexpected failures. It is recommended to follow the manufacturer’s guidelines for lubricant replacement intervals to ensure optimal performance. Additionally, using high-quality lubricants that are compatible with the specific components in your switchgear can also help improve its overall efficiency and reliability.
IV. Safety Precautions
 - Importance of following safety guidelines
Safety precautions are crucial when working with switchgear to prevent accidents and injuries. It is important to always follow safety guidelines provided by the manufacturer and to wear appropriate protective gear, such as gloves and safety goggles, when handling switchgear components. Additionally, make sure to de-energise the equipment before performing any maintenance or inspection tasks to avoid the risk of electrical shock. Regularly inspecting switchgear for any signs of damage or wear, such as frayed wires or loose connections, can help identify potential safety hazards before they escalate. By prioritising safety precautions and following proper procedures, you can help ensure the well-being of yourself and others while working with switchgear.
 - Proper handling of equipment
and adherence to safety protocols are essential to prevent accidents and injuries in the workplace. It is also important to stay up to date on the latest industry standards and regulations regarding switchgear maintenance to ensure compliance and minimise risks. Regular training and communication with team members about safety practices can further enhance the overall safety culture within the organisation. By fostering a proactive approach to safety, employees can work together to create a safe and secure environment for everyone involved in switchgear operations.
 - Use of personal protective equipment
(PPE) is also crucial in maintaining a safe work environment when handling switchgear. Properly fitted gloves, goggles, and other protective gear can help prevent injuries and exposure to hazardous materials. Regular inspections and maintenance of PPE should be conducted to ensure its effectiveness in protecting workers. Additionally, training on the proper use and care of PPE should be provided to all employees to ensure they are equipped to work safely in switchgear environments. By prioritising the use of PPE, companies can further mitigate risks and promote a culture of safety in the workplace.
V. Conclusion
 - Recap of key points discussed
In this paper, it is clear that the use of personal protective equipment is essential in ensuring the safety of workers in switchgear environments. By implementing proper PPE protocols, companies can greatly reduce the risk of injuries and exposure to hazardous materials. Regular inspections, maintenance, and training on the use of PPE are all crucial components in creating a safe work environment. It is important for companies to prioritize the use of PPE and promote a culture of safety to protect their employees. In conclusion, the proper use of PPE is vital in safeguarding workers and preventing accidents in switchgear environments.
 - Importance of regular maintenance
and inspections cannot be overstated. Regular checks on the condition of PPE gear, such as gloves, goggles, and protective clothing, can help identify any wear and tear that may compromise their effectiveness. Additionally, proper maintenance of equipment such as electrical panels and circuit breakers is essential to ensure they are functioning correctly and do not pose a risk to workers. Training on the proper use and maintenance of PPE should be provided to all employees to ensure they are equipped to protect themselves in the event of an emergency. By prioritising regular maintenance and inspections, companies can create a safer work environment and reduce the likelihood of accidents and injuries.
 - Encouragement to seek professional help if needed
It is important for employees to recognise when they may need additional support or assistance in maintaining a safe work environment. If they are unsure of how to properly inspect or maintain equipment, they should not hesitate to seek guidance from a supervisor or trained professional. Seeking help early on can prevent potential hazards from escalating and ensure that the workplace remains safe for all employees. Additionally, if an employee is struggling with the proper use of PPE or feels overwhelmed by safety protocols, they should feel comfortable reaching out for help. Prioritising the well-being and safety of all employees is essential in creating a positive and productive work environment.
Discover more from Tamfis Nigeria Lmited
Subscribe to get the latest posts sent to your email.