Types of Industrial Valves and Calibration Procedures
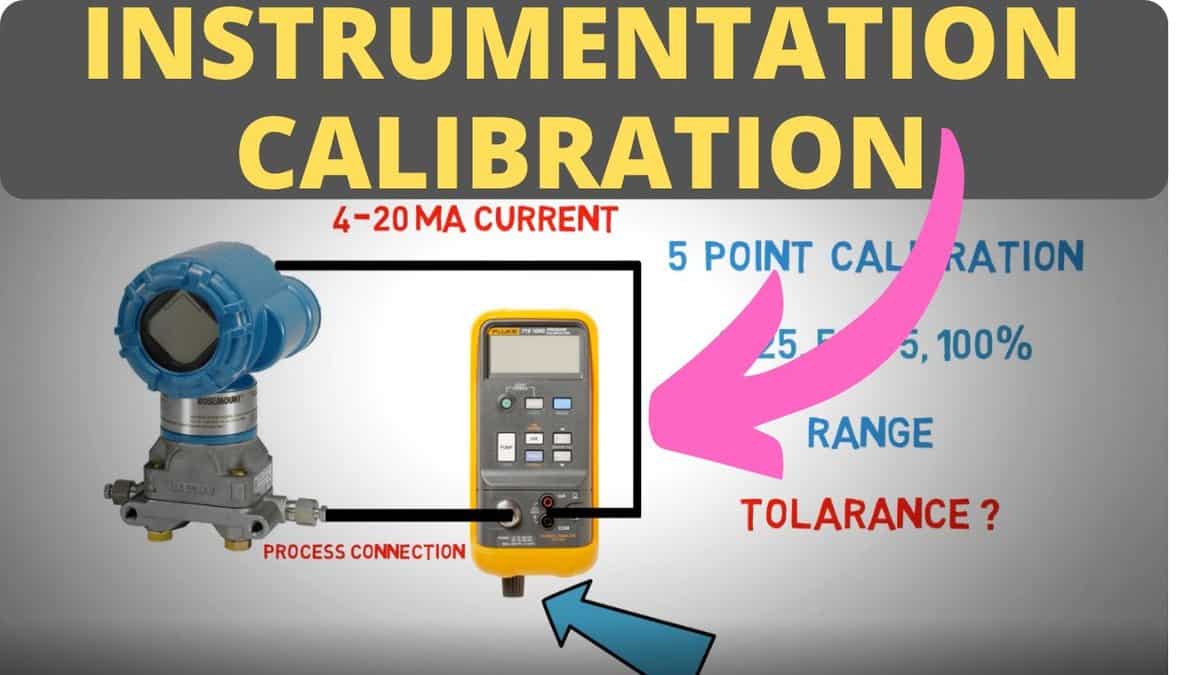
1. Introduction to Industrial Valves
The industrial valve is the name given to the element in different sizes and designs that enable or block the passage of a certain fluid, alter the direction of a flow, regulate the supply, and control the speed, pressure, temperature, and flow of a fluid. Both pneumatic and hydraulic systems are widely used in different areas of the industry, and the promotion of flow regulation becomes indispensable in these situations. The construction of a valve depends on the use for which it will be designed. Fluid pressure, working conditions, and materials used are some of the variables to be taken into account. The study of valves is essential for a good understanding of their operation. It is necessary to understand the functions of the interconnected parts, and the knowledge to be developed can be of great importance in the making of a choice of commercially available valves. Industrial valves are classified into four main technical field categories: isolation, regulation, prevention, retention. Industrial valves play a crucial role in various industries, serving as vital components that allow or prevent the flow of fluids, adjust flow direction, regulate supply, and control factors like speed, pressure, temperature, and flow rate. With the widespread use of pneumatic and hydraulic systems across different sectors, the need for flow regulation has become indispensable. The design and construction of valves depend on their intended applications, considering variables such as fluid pressure, working conditions, and material selection. Studying valves is essential for gaining a comprehensive understanding of their functionality. It is imperative to grasp the interconnected functions of valve parts, as this knowledge can greatly influence the decision-making process when selecting from the wide array of commercially available valves. Industrial valves can be categorized into four primary technical field categories, namely isolation, regulation, prevention, and retention. These categories encompass the diverse roles and purposes that valves serve in industrial settings, highlighting their significance in ensuring operational efficiency and fluid control.
It is up to the preventive industrial valves to protect installations from damage or excessive pressure values. The return industrial valves are responsible for redirecting the fluid in the desired flow. The main methods used to control the flow of the fluid inside the control and direction valves are resistance variation, changing the flow area, stimulation of inertial forces, and interaction between the fluid and energy sources. There are also various types of valves for different uses. Some are normally open, others normally closed by pressure, and others operate both ways. These valves may vary the direction and speed of flow or regulate the flow passage. Since the introduction of hydraulic and pneumatic systems, interest in the study of fluid behavior has been the impetus for the development of various types of valves for different purposes.
Industrial valves play a crucial role in the management and control of fluid flow within various processes across multiple sectors, including water treatment, oil and gas, and chemical manufacturing. At their core, valves regulate the passage of liquids, gases, and slurries, ensuring that systems operate efficiently and safely. The diversity of valve types—ranging from gate and globe valves to butterfly and ball valves—reflects the specific needs inherent to different applications. Proper calibration of these valves is equally essential; it guarantees accuracy and performance, which directly affect the reliability of the overall system. Understanding the various types of valves and their respective calibration procedures lays a foundation for optimizing industrial operations and maintaining regulatory compliance. This essay aims to explore these critical components of industrial engineering, emphasizing both the functionality of valves and the significance of proper calibration techniques in enhancing operational efficacy.
Overview of industrial valves and their significance in various applications
Industrial valves are critical components in a vast array of applications, ranging from water treatment facilities to complex manufacturing processes, playing a pivotal role in controlling fluid flow and pressure within systems. These devices are categorized into various types, including gate, globe, ball, and check valves, each designed to serve specific operational needs and conditions. For instance, ball valves are favored for their ability to provide a quick shut-off, which is essential in safety applications, while globe valves are often used for regulating flow and pressure. The significance of industrial valves extends beyond mere functionality; they impact operational efficiency, safety, and environmental compliance in industries such as petrochemicals and water distribution systems. This is especially evident in water distribution network modeling, where the accuracy and reliability of hydraulic models are heavily reliant on well-calibrated valves to manage leaks and optimize resource management effectively (Sophocleous et al., 2019).
Types of Industrial Valves
Industrial valves play a pivotal role in controlling fluid flow within various systems, with each type designed for specific applications. Among the myriad options available, gate valves are commonly utilized for on-off control, while globe valves excel in regulating flow due to their throttling capabilities. Ball valves, known for their quick operation and reliability, are often favored in applications requiring fast switching. Notably, underwater flat gate valves are crucial in oil and gas extraction, offering advanced sealing technologies that are customizable, as demonstrated by diverse sealing structures for single and split-seat designs. According to a recent report, Underwater flat gate valves play a vital role in oil and gas extraction and deep-sea operations, especially in terms of sealing technology.
Quote 1“Underwater flat gate valves play a vital role in oil and gas extraction and deep-sea operations, especially in terms of sealing technology. With the advancement of technology, the sealing structures of underwater gate valves have become increasingly diversified. Depending on the number of valve seats and the principle of sealing, underwater flat gate valve sealing structures can be classified into single-seat sealing and split-seat sealing.”N/AFurthermore, proper calibration of these valves is essential to maintain operational efficiency and ensure safety in industrial processes.
ValveType UsagePercentage CommonApplications Gate Valve 25 Water supply systems Ball Valve 30 Oil and gas industries Globe Valve 20 Heating and cooling systems Check Valve 15 Pumping systems Butterfly Valve 10 Wastewater management Types of Industrial Valves Data
Classification of valves based on function and design
The classification of valves based on function and design is essential for understanding their applications in industrial settings. Primarily, valves can be divided into two broad categories: control valves and shut-off valves. Control valves, such as globe and rotary valves, are designed to regulate flow rates, pressure, and temperature within a system, providing fine adjustments critical in process control. On the other hand, shut-off valves, including gate and ball valves, are utilized to completely stop or allow the flow of fluid in a pipeline. The design specifics, such as the valves material and internal components, also influence performance and longevity, making it vital for engineers to select appropriate types based on the operational environment and pressure conditions. Furthermore, understanding these classifications aids in developing effective calibration procedures, ensuring optimal functionality of the valve systems within various industrial applications (Krusa et al.), (Macewen et al.).
Calibration Procedures for Industrial Valves
Calibration procedures for industrial valves are essential to ensure accurate operation and compliance with safety standards. The process involves periodic verification of valve performance, which is vital given the increasingly rigorous environmental regulations and the necessity for operational precision in various industrial sectors. Techniques may vary based on valve types, yet all calibration protocols hinge on systematic procedures. As emphasized in the industry, one must follow procedures for calibration and/or performance verification of all equipment, highlighting the critical nature of adherence to established guidelines (quote1). Proper calibration not only enhances reliability but also contributes to the overall efficiency of manufacturing processes, leading to improved sustainability, as well as optimizing material and energy use (cite8). Ultimately, effective calibration procedures directly correlate with the longevity and effectiveness of industrial valves, asserting their importance in the broader context of industrial operations and compliance.
The chart illustrates the calibration frequency in months for various types of valves. The Safety Valve requires the most frequent calibration at every three months, whereas the Check Valve has the longest interval at eighteen months. Other types, such as the Ball Valve, Globe Valve, and Gate Valve, require calibration intervals of six, nine, and twelve months respectively. This data highlights the varying maintenance needs of different valves in industrial applications.
Importance of calibration and standard methods used in the industry
In the realm of industrial processes, the importance of calibration and standardized methods cannot be overstated, particularly in relation to the functionality and reliability of industrial valves. Calibration ensures that measurement instruments and control systems operate within specified limits, thereby enhancing efficiency and safety in operations. Accurate calibration practices, such as those outlined in certification programs, contribute to the overall integrity of pressure vessels and associated systems ((Krusa et al.)). Furthermore, advancements in technology, such as micro-electrical-mechanical systems (MEMS), have underscored the necessity of calibration by enabling precise measurements and monitoring of conditions within multi-channel evaporators and heat pumps ((Hrnjak et al., 1998)). Without rigorous calibration protocols, the risk of maldistribution and inefficiencies increases, potentially leading to operational failures and safety hazards. Consequently, adherence to standardized calibration methodologies plays a crucial role in maintaining performance consistency and regulatory compliance across various industrial applications.
Conclusion
In conclusion, understanding the various types of industrial valves and their calibration procedures is critical for optimizing system performance and ensuring operational efficiency. The implementation of advanced technologies, such as micro-electrical-mechanical systems (MEMS), illustrates a significant leap in valve calibration and monitoring, particularly in complex applications like multi-channel evaporators. For instance, MEMS sensors have been demonstrated to effectively identify refrigerant maldistribution, thereby enhancing the reliability and efficacy of industrial processes ((Hrnjak et al., 1998)). This evolution in calibration practices not only contributes to energy savings and reduced waste but also aligns with modern demands for precision in industrial operations. Ultimately, as industries increasingly adopt sophisticated valve technologies coupled with thorough calibration procedures, they will be better positioned to tackle the engineering challenges of the future while adhering to sustainability goals and improving overall system integrity. Thus, the integration of these methodologies is imperative for continuous improvement in industrial applications.
Summary of key points and the impact of proper valve selection and calibration on industrial efficiency
In summary, the selection and calibration of valves play a crucial role in enhancing industrial efficiency, directly impacting operational effectiveness and cost management. Proper valve selection entails choosing the right type for specific applications, which includes evaluating factors such as pressure, temperature, and flow requirements. Each valve type—be it a globe, ball, or butterfly valve—has distinct advantages and limitations that must align with the processs operational demands. Furthermore, accurate calibration ensures that valves function optimally, facilitating precise control over fluid dynamics. This control is essential for minimizing leaks and system downtime, ultimately leading to increased productivity. When valves are appropriately selected and calibrated, industries can achieve significant energy savings and reduced waste, which are critical for maintaining competitiveness in today’s market. Consequently, the integration of comprehensive valve management strategies bolsters overall operational resilience and sustainability in industrial settings.
References:
- Hrnjak PS, Leicht TM, Shannon, Mark A. (1998). Exploratory Research on MEMS Technology for Air-Conditioning and Heat-Pumps. Air Conditioning and Refrigeration Center. College of Engineering. University of Illinois at Urbana-Champaign., https://core.ac.uk/download/4822380.pdf (Accessed: 10 Dec, 2024).
- Chen, Chuxin, Marapane, Suresh, Trivedi, Mohan M. (2024). Automatic inspection of analog and digital meters in a robot vision system. https://core.ac.uk/download/pdf/42829912.pdf (Accessed: 10 Dec, 2024).
- Huang B, Shah SL, Thornhill NF,. (2001). Detection of distributed oscillations and root-cause diagnosis. https://core.ac.uk/download/1669185.pdf (Accessed: 10 Dec, 2024).
- Fricks D,H, Jeffers E,L, Taylor R,E. (2024). NASA JSC water monitor system: City of Houston field demonstration. https://core.ac.uk/download/pdf/42869066.pdf (Accessed: 10 Dec, 2024).
- Sophocleous S,. (2019). Development of the Next Generation of Water Distribution Network Modelling Tools Using Inverse Methods. College of Engineering, Mathematics and Physical Sciences, https://core.ac.uk/download/219598955.pdf (Accessed: 10 Dec, 2024).
- Krusa, Paul W, Lundy, Floyd. (2024). Guide for certifying pressure vessels and systems. https://core.ac.uk/download/pdf/42806102.pdf (Accessed: 10 Dec, 2024).
- Macewen J,D, Vernot E,H. (2024). Toxic Hazards Research Unit. https://core.ac.uk/download/pdf/80649185.pdf (Accessed: 10 Dec, 2024).
- Milošević, Miloš, Mitrović, Nenad, Momčilović, Nikola, Petrović, Aleksandar, Popović, Dejana. (2020). Sustainable development of pressure equipment using 3d digital image correlation method. ‘National Library of Serbia’, https://core.ac.uk/download/553149974.pdf (Accessed: 10 Dec, 2024).